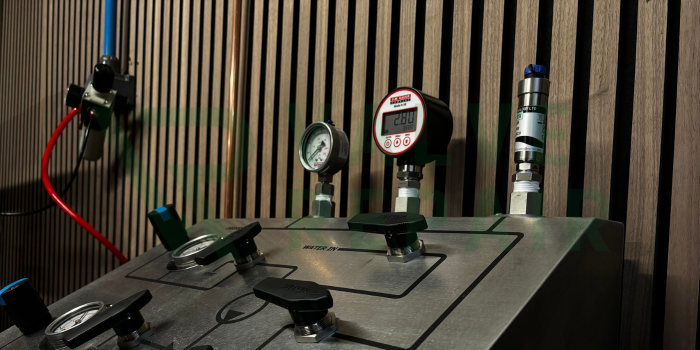
Chemical
In the chemical industry, valves must withstand corrosive substances, extreme temperatures, and high pressures. A faulty valve can lead to safety hazards, production downtime, and costly product loss.
Common Valve Issues in Chemical Processing:
- Corrosion from acidic and caustic chemicals
- Erosion from abrasive slurries and particulates
- Pressure drops caused by valve degradation
- Failure to meet ATEX and hazardous area safety standards
Why Choose Us for Chemical Valve Repair?
- Specialist refurbishment for chemically resistant materials
- Testing and repairs compliant with hazardous environment regulations
- Emergency repair services to prevent production halts
We support chemical plants, refineries, and hazardous material processing with expert valve restoration.
How it works...
Types of Valves we repair
-
Ball Valves
Ball valves play a crucial role in process control, offering tight shut-off and minimal pressure drop. Over time, seal degradation, corrosion, and internal wear can lead to leaks and operational inefficiencies.
-
Butterfly Valves
Butterfly valves are widely used in steam, water, and industrial flow applications, but seat wear, disc misalignment, and actuator failures can impact their performance.
-
Gate Valves
Gate valves are designed for on/off flow control but can suffer from seat erosion, corrosion, and sticking mechanisms over time.
-
Globe Valves
Globe valves are essential for flow modulation and throttling applications, but plug and seat wear, erosion, and actuator issues can reduce efficiency.
FAQ's
What is valve pressure testing, and why is it important?
Valve pressure testing is a quality control process that ensures your valves can withstand operational pressures without leaking or failing. It helps prevent costly breakdowns, safety hazards, and system inefficiencies, ensuring your valves perform reliably under real-world conditions.
What types of pressure testing do you offer?
We offer three main types of pressure testing:
- Hydrostatic Testing – Uses water to check for leaks and structural integrity.
- Pneumatic Testing – Uses compressed air or gas to detect even the smallest leaks.
- Seat Leak Testing – Ensures a tight seal when the valve is closed, preventing internal leakage.
How often should valves be pressure tested?
The frequency of pressure testing depends on the type of valve, application, and industry regulations. In critical applications such as steam, oil & gas, and chemical processing, valves should be tested at regular intervals to ensure ongoing reliability and compliance with safety standards.
What happens if my valve fails the pressure test?
If a valve fails testing, we provide a detailed failure report outlining the issue. Our team can then recommend repairs, refurbishment, or replacement parts to restore the valve to full working condition, ensuring it meets performance and safety requirements