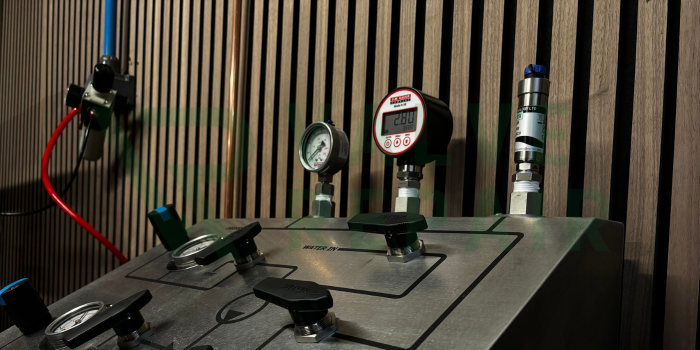
Emergency Valve Repair
Emergency Valve Repair – Fast, Reliable, and Minimising Downtime
When a valve failure occurs, every second counts. At Valve Repair, we provide rapid-response emergency valve repair services to get your operations back online as quickly as possible. Whether it’s a critical leak, a seized valve, or a complete breakdown, our expert team is ready to assess, repair, and restore your valve’s functionality with minimal disruption.
Valve failures can cause production shutdowns, safety hazards, and costly delays. Our emergency repair service ensures that your faulty valve is fixed fast, preventing unnecessary downtime and protecting your business from operational losses.
Why Choose Our Emergency Valve Repair Service?
- Rapid Response & Fast Turnaround – We understand the urgency of valve failures and act quickly to restore function.
- On-Site or Workshop Repairs – Depending on the situation, we provide both on-site diagnostics and workshop-based solutions.
- All Valve Types & Manufacturers Covered – We repair ball, butterfly, gate, globe, control, and safety valves from all major brands.
- Cost-Effective Alternative to Replacement – Emergency repair helps avoid costly new valve purchases and keeps your equipment running.
- Industry Expertise & Quality Assurance – Every repair undergoes rigorous testing to ensure safety, durability, and compliance with operational standards.
Common Emergency Valve Issues We Fix
- Leaking or Damaged Seals – Preventing fluid loss and pressure drops.
- Sticking or Seized Valves – Restoring smooth operation and full movement.
- Actuator or Control Failures – Ensuring proper automation and response times.
- Corrosion & Wear Damage – Replacing or refurbishing worn components for longevity.
- Pressure Loss & Performance Issues – Diagnosing and resolving inefficiencies to maintain optimal system performance.
Our Emergency Valve Repair Process
1. Immediate Diagnosis & Fault Assessment
- Rapid on-site inspection to identify the root cause of failure.
- Pressure testing, leak detection, and functional assessments.
2. Fast Repair & Component Replacement
- Immediate replacement of seals, seats, gaskets, and critical components.
- Precision machining and reconditioning if needed.
- If a full replacement is required, we provide temporary solutions to keep your system running.
3. Testing & Quality Assurance
- Hydrostatic and pneumatic pressure testing to ensure the repair is effective.
- Leak-tight verification and operational checks before reinstallation.
- Performance validation to prevent repeat failures.
How it works...
Types of Valves we repair
-
Ball Valves
Ball valves play a crucial role in process control, offering tight shut-off and minimal pressure drop. Over time, seal degradation, corrosion, and internal wear can lead to leaks and operational inefficiencies.
-
Butterfly Valves
Butterfly valves are widely used in steam, water, and industrial flow applications, but seat wear, disc misalignment, and actuator failures can impact their performance.
-
Gate Valves
Gate valves are designed for on/off flow control but can suffer from seat erosion, corrosion, and sticking mechanisms over time.
-
Globe Valves
Globe valves are essential for flow modulation and throttling applications, but plug and seat wear, erosion, and actuator issues can reduce efficiency.
FAQ's
What is valve pressure testing, and why is it important?
Valve pressure testing is a quality control process that ensures your valves can withstand operational pressures without leaking or failing. It helps prevent costly breakdowns, safety hazards, and system inefficiencies, ensuring your valves perform reliably under real-world conditions.
What types of pressure testing do you offer?
We offer three main types of pressure testing:
- Hydrostatic Testing – Uses water to check for leaks and structural integrity.
- Pneumatic Testing – Uses compressed air or gas to detect even the smallest leaks.
- Seat Leak Testing – Ensures a tight seal when the valve is closed, preventing internal leakage.
How often should valves be pressure tested?
The frequency of pressure testing depends on the type of valve, application, and industry regulations. In critical applications such as steam, oil & gas, and chemical processing, valves should be tested at regular intervals to ensure ongoing reliability and compliance with safety standards.
What happens if my valve fails the pressure test?
If a valve fails testing, we provide a detailed failure report outlining the issue. Our team can then recommend repairs, refurbishment, or replacement parts to restore the valve to full working condition, ensuring it meets performance and safety requirements